Classes of Stainless Steel: Austenitic, Ferritic, and Martensitic
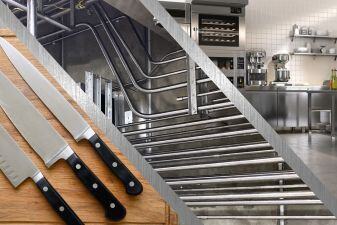
Stainless steel has become a top material choice across various industries and applications from kitchen utensils and appliances to medical instruments and exhaust systems. With such a wide range of uses, it poses the question: Are all stainless steels the same?
While some characteristics are universal, stainless steels can be broken down into three classes: austenitic, ferritic, and martensitic. The class of stainless steel chosen for a specific application is based on the requirements of the application as well as the evaluation of performance against cost and manufacturability. In the electrical industry, conduit and fittings are made from austenitic stainless steel.
The three classifications are based on the microstructure and metallic crystal structure of the alloy. Microstructure refers to the size and shape of the grains of metal formed as the metal cools and solidifies; the metallic crystal structure is the arrangement of the atoms in the metal. The microstructure and crystal structure help define the characteristics and mechanical properties of each classification.
Austenitic
Austenitic stainless steels include the common grades of 304, 316 and 310. They provide the best corrosion resistance of the three classes and offer the best mechanical properties over a wide temperature range, including low temperatures. Austenitic stainless steels have good ductility (making them formable and easy to fabricate). They also show little to no magnetism.
Ferritic
Ferritic stainless steels such as 409, 430, 439 are more economical with a lower weight % of nickel and provide decent corrosion resistance. However, they can become brittle at low temperatures (e.g., below 32°F) and have reduced ductility, making them harder to form and weld, especially in thicker cross sections. Ferritic stainless steels are magnetic, which can be an advantage in some non-electrical applications such as for refrigerators.The ferritic class can be a good compromise for applications such as appliances and exhaust systems that can be executed with thinner cross sections and are highly price sensitive/commoditized.
Martensitic
Martensitic stainless steels, such as 420 and 440, have the greatest strength. They can be hardened by heat treating, unlike the other two classes. This combination makes them good for applications requiring wear resistance like cutting tools and knives. However, their strength is offset by brittleness at low temperatures and the lowest corrosion resistance of the three classes.
Class Comparison:
The main alloying elements and strength characteristics of the three classes can be found below. These drive each class’s performance and cost difference.
Properties | Austenitic | Ferritic | Martensitic |
---|---|---|---|
Chromium content | 16 - 25% | 11 - 30% | 11.5 – 18% |
Nickel content | 6 – 22% | 0 – 0.5% | 0 - 2.5% |
Tensile Strength at Room Temperature | 29 – 87 ksi | 58 – 87 ksi | 101.5 – 290 ksi |
Gibson Products
Gibson Stainless products are offered in Type 304 and Type 316 stainless steel and are therefore considered to be austenitic, providing the best corrosion resistance in harsh environments. This class provides high ductility and toughness at both high and low temperatures, allowing them to perform well in a wide array of environments including cold rooms / freezers in food and beverage applications as well as hot and cold outdoor environments from coastal Alaska to the Gulf of Mexico. These characteristics ensure that Gibson’s electrical conduit systems will have a long service life, reducing the need for costly replacements or repairs.